Ore Grade Scanner
Transforming Mining Efficiency and Sustainability
Ore bodies are inherently variable, with grade heterogeneity influenced by factors such as ore deposit characteristics, mining methods, material handling, crushing, and blending processes prior to processing. This natural variability can significantly impact product quality, recovery rates, and overall profitability—often resulting in losses amounting to millions of euros annually.
Current mining practices typically aim to blend this variability into a consistent feed for processing plants. However, this often comes at the cost of lower mineral recovery rates.
Our Solution
To enhance efficiency and profitability, real-time ore sorting and ore grade blending offer a more effective approach.
Advances in sensor technologies now enable accurate, real-time ore classification, delivering significant benefits at the early stages of mining—either before or after primary crushing.
Early-stage ore grade control is substantially more efficient than later-stage processing. At this point, ore remains unmixed and less fragmented, making grade determination more accurate and reducing the need for complex or expensive equipment.
Unlock New Opportunities Across Mines and Quarries
OreScanner provides real-time measurements of clay, limestone, dolomite, quartz, and other mineral content.
It empowers mining and quarry operations with actionable insights to optimize stockpiling, minimize waste, and control ore blending 24/7—enabling faster, smarter, and more sustainable operations.
How It Works
OreScanner is installed above a conveying system—such as a conveyor belt, apron feeder, or discharge chute—where it continuously measures ore quality in real time. As material moves beneath the sensor array, the system calculates the average ore grade per user-defined batch, with batch size configurable from around 100 kg to a full truckload. This enables informed, real-time decisions about how to handle each batch.
Ore Sorting
If the plant is set up with multiple stockpiles, silos, or processing lines, OreScanner is used to sort ore based on grade. For example, high-grade material might go to the main processing line, medium-grade to a secondary line, and low-grade or waste to separate piles. In other operations, ore may simply be split into “production ore” and “waste ore.” This sorting helps maximize recovery, reduce dilution, and cut energy use by keeping low-value material out of the plant.


Smart Ore Blending
If only one stockpile or production line is available, OreScanner supports smart blending by continuously measuring ore quality in real time and calculating the cumulative grade of the entire stockpile. If the cumulative grade begins to fall below the target, the automation system can request high-grade material from a designated blast pile. If it exceeds the target, it calls for low-grade material instead. This enables consistent feed quality, minimizes processing issues, and helps maintain optimal plant performance.
OreScanner is especially useful in operations where ore quality varies within a single blast or where high-grade veins are mixed with waste zones. Detecting these differences in real time helps prevent dilution and supports better, more profitable decisions in the field.
Key Benefits
The advantages of real-time grade control depend on the specific ore type and operation setup, but typical benefits include:
Increased Ore Recovery:
Reduces low-grade ore waste by up to 25%, maximizing resource utilization and increasing operational revenue.
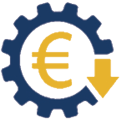
Improved Product Quality:
Decreases the standard deviation of raw material quality by up to 20%, ensuring stable processing and consistent final product quality that meets client specifications.
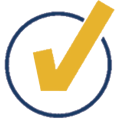
Lower Fuel and Energy Consumption:
Reduces fuel and energy usage in calcination and beneficiation processes by up to 15%, resulting in substantial cost savings and supporting more sustainable operations.
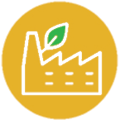
Don't Let Valuable Resources End Up in Waste Piles
Discover the Difference — Explore Our Customer Case Studies